As the warm weather and humidity return to our region, the issue that inevitably resurfaces every year is mold on wood packaging.
Mold is a concern for some end user food-grade customers and occasionally customers who are very particular about the appearance of wood packaging for the shipping of their product. In order for mold to grow, appropriate conditions of oxygen, a food source and moisture must be present. One of those three conditions must be restricted to prevent the growth of mold. Mold spores are in the air around us all the time. They are just looking for the perfect place to grow and wood packaging can be an ideal place for that growth.
The purpose of this article is to inform end users of the 3 most commonly discussed issues during routine service calls where mold has been raised as a possible concern. They are as follows:
- Is it really mold;
- The steps your vendor could be taking to prevent mold during the manufacture of wood packaging;
- Best practices for taking the proper measures to prevent mold once the wood packaging is at the customer location.
Is It Really Mold?
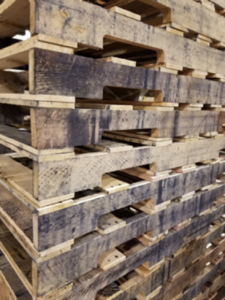
Often times we receive calls about moldy product from the customer. More times than not, it is something else entirely. There are other naturally occurring forms of discoloration that may look like mold, but aren’t biological in nature. Thus, the product is completely safe to use in an environment that is sensitive to food grade issues. These discolorations could include iron stain, blue stain, brown stain, sun exposure, enzymatic discolorations and mineral discolorations.
A great resource on these discolorations and what they are can be found at www.naturespackaging.org.
Prevention Measures by the Packaging Professional
As stated earlier, the main factors that promote the growth of mold on wood packaging are moisture, appropriate amounts of oxygen and food source, i.e. the wood. Our best chances at preventing mold are limiting the moisture on and around the packaging. The two proven methods of preventing mold are chemical treatments and/or preventative measures. Heat treating is not a viable solution for preventing mold. It inherently draws moisture and sugar (food source) to the surface of the wood which can provide an ideal environment for the growth of mold. Heat treatment is explicitly used for export purposes and will kill bugs and microorganisms.
As stated, there are chemicals on the market that prevent mold from growing on the wood packaging. One leading product works by sealing the wood from oxygen. The effectiveness of chemical treatments can range from a few weeks to 3 months, depending on the circumstances of storage and environment over time. Application of the chemicals can be prohibitive for some pallet and wood packaging suppliers and thus not an option. Chemical treatments aren’t approved or disapproved by the FDA, so using these methods are completely at the discretion of the end user and their respective comfort levels in using chemical applications.
Most packaging suppliers use preventative measures for limiting the potential for mold. The easiest way to keep mold under control is the use of kiln dried lumber where moisture content is below 18%. Typically, kiln dried wood used in wood packaging is either Southern Yellow Pine (SYP) or Spruce Pine Fir (SPF). There are some manufacturer’s that may be able to obtain kiln dried hardwoods, but that’s not typically used in wood packaging, mostly due to cost considerations. It’s most economical to use either KD SYP or KD SPF. Just because your manufacturer is buying kiln dried materials doesn’t insure mold won’t appear on the wood. Additional preventative practices for insuring mold doesn’t grow would be keeping moisture off the wood. Additional methods should be incorporated and could include wrapping the bundles of wood in a moisture barrier paper, storing the bundles inside, using fans to generate air flow and storing finished goods inside prior to shipment to the end user.
Tips for Preventing Mold at Your Location
Once the wood packaging leaves our facility, we begin to lose control over using preventative procedures to prevent mold of the finished packaging. Our best practice to prevent mold at this time is customer education. Our typical points of contact, i.e. purchasing agents, facilities coordinators or corporate buyers, typically aren’t the people handling wooden packaging at their respective locations. It’s imperative that our account personnel stress the importance of a team approach to inform all handlers of the wood packaging about mold, material choices and the storage conditions after receiving the finished goods on-site.
Our recommendations are relatively simple, but they can be the difference in mold prevention. They are as follows:
- If the customer is going to store pallets in trailers, be sure to open the rear doors. Air flow is critical. After a few days in the humidity with a completely enclosed trailer, we often receive a phone call that the wood packaging is moldy. Opening the doors at receipt of the load isn’t full proof, but it really goes a long way in mold prevention.
- If you’re storing your wood packaging indoors, do so in a location that has some air flow. Mold spores are airborne and they prefer “still” air to adhere to a surface and begin the process of growth.
- Store your wood packaging in a dry environment. It lowers the risk for mold to grow. This suggestion compounds with the idea of air flow, which will speed up the process of drying out wooden packaging that has high moisture content.
- Heat also promotes the growth of spores, so discussing options for storage in a cool spot within the facility is also very helpful.
Applying these recommendations takes care of the majority of our customer located mold issues. When doing so, we find fewer customer complaints that require the need to trouble shoot causes and concerns in regards to mold. The key to success is communication and setting realistic expectations. If an issue does occur, being pro-active in eliminating the mold from the pallets is essential. We typically use a bleach/water mix to spray the pallets if an issue occurs.
For some customers, the cost savings benefit of “green” high moisture soft wood outweighs the potential for mold on the packaging. In any application, your packaging professional should be taking the time to understand the application, use tested knowledge to analyze the environment, and recommend wood materials best suited for your downstream application.
Please visit our sites at www.jfrohrbaugh.com or www.westsidewoodproducts.com for more information and additional helpful articles concerning our industry’s standards, news and education. In addition, www.naturespackaging.org provides a number of related articles to the realm of mold and best practices in prevention.